Dextra is pleased to announce its patron membership with the International Institute for FRP in Construction (IIFC), a globally recognized organization dedicated to the advancement of Fiber-Reinforced Polymer (FRP) composites in the construction industry. This partnership underscores Dextra’s commitment to innovation, sustainability, and the development of next-generation structural reinforcement solutions.
What is IIFC and How It Supports the Industry
The International Institute for FRP in Construction (IIFC) is a leading global organization that promotes the use of FRP composites for civil infrastructure. Through a combination of research initiatives, educational programs, and industry collaborations, IIFC plays a pivotal role in driving the adoption of FRP solutions. Its key activities include:
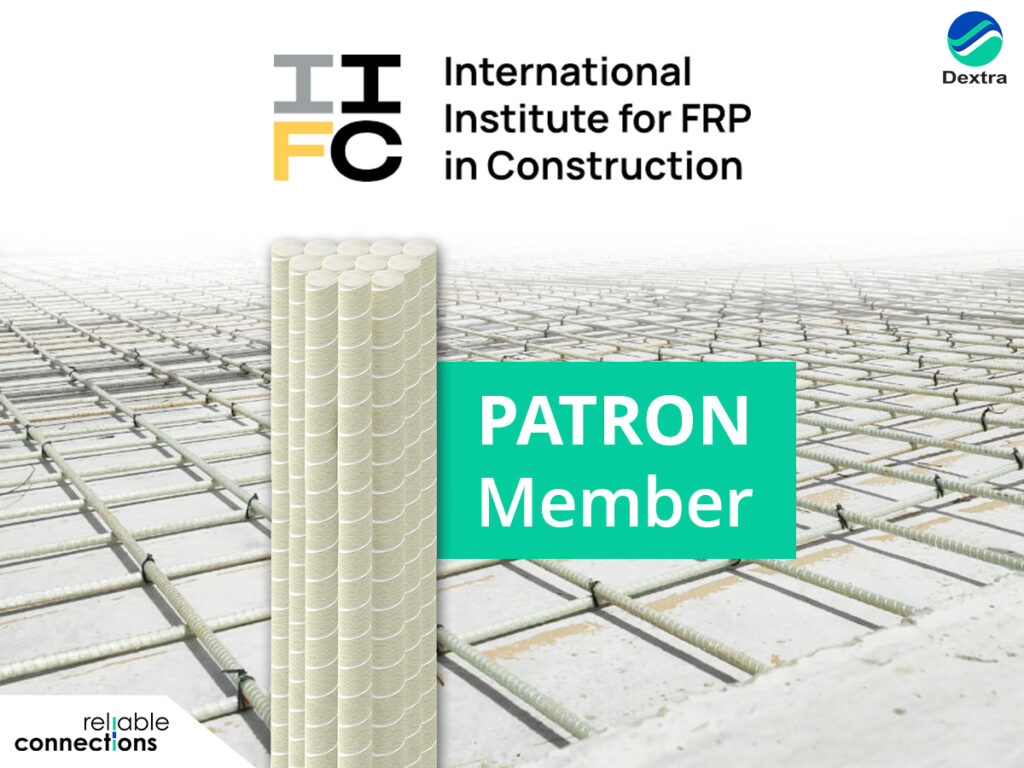
- Facilitating Knowledge Sharing: IIFC organizes conferences, workshops, and symposiums where researchers, engineers, and industry professionals exchange the latest findings and best practices.
- Developing Standards and Guidelines: By working closely with standard-setting bodies, IIFC helps ensure that FRP technologies meet rigorous performance and safety requirements, paving the way for broader industry acceptance.
- Encouraging Collaborative Research: IIFC fosters partnerships between academia and industry to push the boundaries of FRP innovation, focusing on both fundamental research and applied engineering solutions.
By offering a platform where experts can collaborate, IIFC contributes significantly to the advancement and standardization of FRP technologies, ultimately benefiting the construction industry and society at large.
Why FRP Matters in Modern Construction
As the industry moves toward more sustainable and durable infrastructure solutions, FRP composites have emerged as a game-changing material. Offering superior corrosion resistance, high strength-to-weight ratios, and extended service life compared to traditional steel reinforcements, FRP is being increasingly adopted in critical construction applications worldwide.
With growing concerns about the environmental impact and longevity of reinforced concrete structures, FRP presents a solution that significantly reduces maintenance costs and enhances resilience in harsh environments, such as marine, transportation, and industrial infrastructure.
Dextra’s Commitment to FRP Innovation
Dextra has long been at the forefront of developing advanced reinforcement solutions, including our Durabar+ GFRP Rebar, which recently earned ICC-ES certification for compliance with international building standards. By joining IIFC as a Patron Member, Dextra strengthens its role in shaping the future of FRP applications through research collaboration, knowledge sharing, and contribution to industry’s best practices.
Through this partnership, Dextra will actively engage with leading researchers, engineers, and policymakers to support the widespread adoption of FRP materials in construction projects worldwide.
What This Means for the Future
By joining forces with IIFC, Dextra continues to lead the way in providing high-performance reinforcement solutions that meet the evolving needs of modern construction. Our participation will drive:
Greater industry awareness of FRP’s advantages and applications
Collaborative research initiatives to further validate FRP solutions
Stronger regulatory and standardization efforts for FRP in structural applications
A sustainable future with durable, corrosion-resistant construction materials
Looking Ahead
At Dextra, we are excited to embark on this journey with IIFC and contribute to the ongoing transformation of the construction industry. As FRP adoption continues to grow, we remain committed to delivering high-quality reinforcement solutions that support resilient and environmentally responsible infrastructure.
For more information about IIFC and its mission, visit: www.iifc.org
Stay connected with Dextra for more updates on our innovations in FRP technology!