Dextra is pleased to announce that Durabar+ GFRP rebar has successfully achieved ICC Evaluation Service (ICC-ES) confirmation, demonstrating compliance with the 2024, 2021, and 2018 International Building Code (IBC) and International Residential Code (IRC).
This confirmation, detailed in ICC-ES evaluation report ESR-5501, provides essential guidance to code officials, engineers, and contractors for approving the use of Durabar+ in accordance with these standards. The evaluation follows the Acceptance Criteria for Fiber-reinforced Polymer (FRP) Bars and Meshes for Internal Reinforcement of Non-structural Concrete Members (AC521).
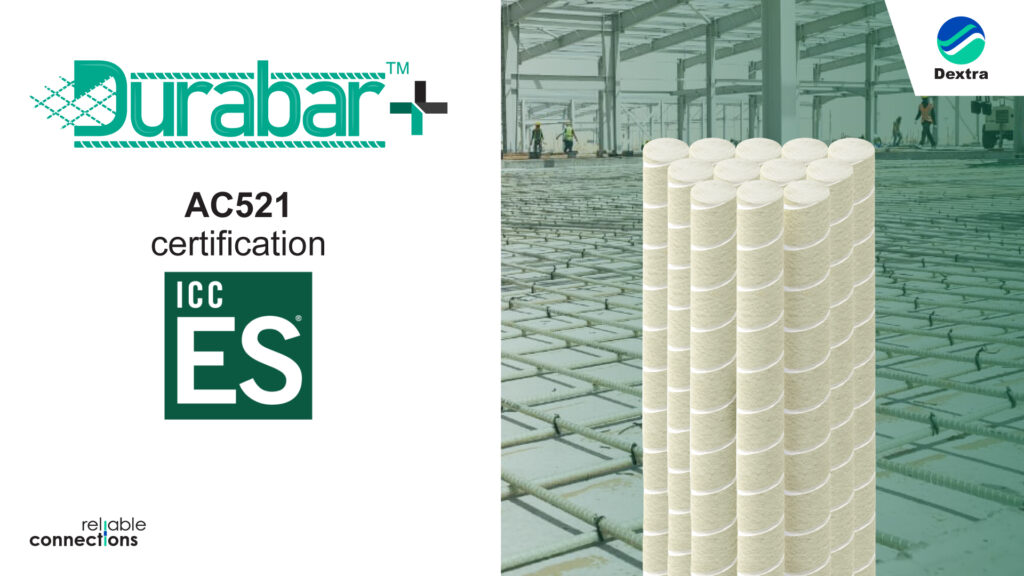
What It Means for the Construction Industry
Code Compliance: With this recognition, Durabar+ is officially verified for use in building and residential construction under major international codes.
Corrosion Resistance: As a non-metallic reinforcement, Durabar+ is ideal for applications where traditional steel rebar faces durability challenges, such as in coastal, marine, and chemically aggressive environments.
Lightweight & High Strength: Offering exceptional tensile strength with a lighter weight than steel, Durabar+ enhances constructability and reduces handling costs.
Why is the ICC-ES AC521 Certification Important?
The AC521 certification is a significant recognition that validates the quality, safety, and compliance of FRP bars and meshes in construction. It ensures that these materials meet strict evaluation criteria, allowing them to be confidently used in projects that require durable, non-corrosive reinforcement.
Key Benefits for Our Customers
By eliminating corrosion concerns and reducing maintenance costs, Durabar+ GFRP rebar aligns with the industry’s push toward sustainable, long-lasting infrastructure solutions. This ICC-ES evaluation further cements its position as a reliable and innovative alternative to conventional steel reinforcement.
Verified Performance – ICC-ES certification confirms that the mechanical properties of our product align with the data in our Product Data Sheet (PDS).
Regulatory Compliance – Our FRP rebar meets ACI 440.1R design standards, providing engineers with confidence in their calculations.
Safety & Quality Assurance – Independently tested to meet industry regulations, ensuring durability and reliability.
Cost Efficiency – Standardized, certified materials simplify project specifications, leading to streamlined procurement and reduced risks.
Who Should Be Interested?
This certification is highly relevant for: Construction and Infrastructure Professionals – Ensuring project compliance with certified, high-performance reinforcement.
Structural Engineers & Designers – Using Durabar+ confidently in calculations and structural designs.
Regulatory Authorities & Code Enforcers – Supporting the industry’s shift towards standardization and advanced materials.
Building the Future with Certified Innovation
Durabar+ is our advanced GFRP rebar solution, engineered with ISO polyester resin and E-CR glass fibres for superior performance in reinforced concrete applications. Designed to withstand harsh environments, Durabar+ offers exceptional corrosion resistance, high tensile strength, and long-term durability, making it an ideal alternative to traditional steel reinforcement in infrastructure and marine projects.
With ICC-ES AC521 certification, Durabar+ GFRP Rebar is set to drive the adoption of sustainable, corrosion-resistant reinforcement in modern construction.
Interested in integrating Durabar+ into your next project? Contact us today to learn more!